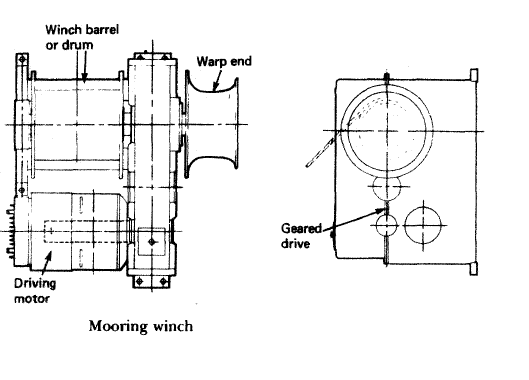
Figure : Deck mooring winch
Most deck machinery is idle during much of its life while the ship is at sea. In
port, cargo equipment will be in use for one or more days but the machinery for
anchoring and mooring is used for a very limited time. Deck machinery with a
restricted and intermittent duty may be designed with drives with a rating
limited from 30 minutes to one hour. Despite long periods of idleness, often in
severe weather conditions, machinery must operate immediately, when
required. Cooling vents, open when machinery is working, must be closed for
the sea passage.